Businesses across industry verticals are looking for ways to cut costs while improving efficiency. This is especially true for the chemical industry, where managing production costs can be a challenge due to the complexity of the processes.
One powerful tool that many chemical companies are using to address this challenge is SAP Business One. This software helps businesses streamline their operations, improve efficiency, and reduce production costs.
In this blog, we’ll explore how SAP B1 for chemical product reduction can help chemical companies cut costs and improve productivity. We’ll also highlight the benefits of using an ERP system, like SAP Business One, specifically designed for the chemical industry.
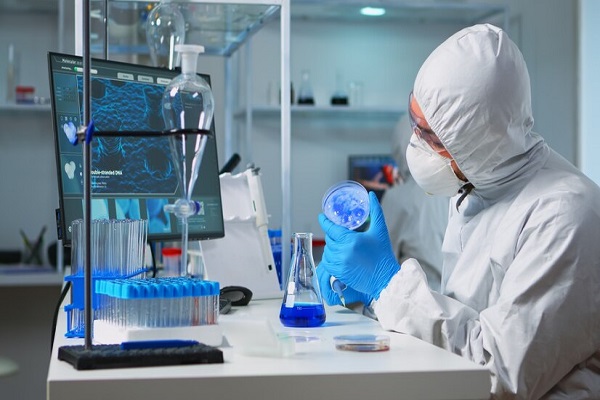
What is SAP Business One?
SAP Business One is a business management software solution that helps small and medium-sized businesses run more efficiently. It’s an ERP system that allows businesses to manage all their core operations from a single platform. This includes finance, sales, customer relationships, inventory, and production.
ERP for the chemical industry is crucial because it helps manage the complex processes involved in production, from sourcing raw materials to manufacturing and distributing products.
Challenges in the Chemical Industry
Chemical production is a multi-stage process that involves handling hazardous materials, strict regulations, and fluctuating costs of raw materials. Managing all these factors efficiently while keeping production costs low can be difficult. Without the right tools, companies might face issues like:
- Inefficient inventory management
- Difficulty in tracking raw material costs
- Compliance with strict safety regulations
- Delays in production due to lack of real-time data
This is where SAP Business One comes into play. By providing a centralized platform to manage all aspects of the business, SAP B1 for chemical product reduction can help overcome these challenges.
How SAP Business One Helps Reduce Production Costs
Better Inventory Management
One of the biggest challenges in the chemical industry is managing inventory. Chemicals have a limited shelf life, and storing them for too long can lead to waste. With SAP Business One, companies can track their inventory in real time. This helps reduce excess stock, minimize waste, and cut storage costs.
By having better control over inventory, businesses can also avoid stockouts, which can cause production delays. This is a great example of how reducing production costs with ERP can be easily achieved.
Real-Time Data and Decision Making
In the chemical industry, making quick decisions is critical. Whether ordering raw materials or adjusting production schedules, delays can cost a lot of money. With SAP Business One, companies get access to real-time data, which helps them make informed decisions faster.
This real-time data allows businesses to adjust their production processes based on demand, reducing the risk of overproduction and saving money. This is why SAP for chemical production is becoming increasingly popular among manufacturers.
Compliance with Safety and Environmental Regulations
The chemical industry is highly regulated, with strict safety and environmental standards. Failing to comply with these regulations can result in costly fines and damage to the company’s reputation.
SAP Business One helps chemical manufacturers stay compliant by providing tools to manage safety data sheets, hazardous materials, and regulatory requirements.
By using chemical manufacturing ERP solutions like SAP B1, companies can ensure they meet all regulatory requirements, avoid fines, and maintain a safe working environment.
Streamlined Production Processes
Another key benefit of SAP Business One Implementation is that it helps streamline production processes. The software can automate many manual tasks, such as order processing and production scheduling, reducing the risk of errors and saving time.
By streamlining these processes, companies can increase productivity and reduce labor costs. This is a significant advantage for companies looking to reduce production costs with ERP.
The Role of SAP Implementation Partners
To get the most out of SAP Business One, it’s essential to work with a qualified SAP B1 partner. These partners help businesses implement and customize the software to meet their needs.
A trusted SAP implementation partner can provide expert guidance throughout the implementation process, from choosing the right modules to training employees on how to use the software. They can also help companies stay within budget by providing transparent pricing information, including the SAP Business One price.
Working with an experienced SAP Business One solution provider can ensure a smooth implementation and help businesses start reaping the benefits of the software as quickly as possible.
Why Chemical Manufacturers Are Turning to SAP Business One
The chemical industry is constantly evolving, and companies need to adapt to changes quickly. Whether it’s new regulations, rising raw material costs, or changing customer demands, SAP Business One for chemical product reduction offers a flexible solution that can grow with the business.
Companies can gain greater control over their operations by implementing chemical manufacturing ERP solutions like SAP B1, reduce waste, and improve profitability. The software provides the tools to streamline production processes, manage inventory more effectively, and ensure compliance with all industry regulations.
Conclusion
Reducing production costs is essential for chemical manufacturers to remain profitable in today’s competitive market. SAP B1 for chemical product reduction is a powerful tool that can help businesses achieve this by improving inventory management, providing real-time data, ensuring regulatory compliance, and streamlining production processes.
Also Read: CEO’s Guide to Implementing ERP for Manufacturing Expansion
Working with a trusted SAP B1 partner, like Praxis Info Solutions, can make the implementation process smoother and more effective. By leveraging the power of ERP for the chemical industry, businesses can stay ahead of the competition and continue to grow.
If you’re looking to reduce costs and improve efficiency in your chemical manufacturing business, consider implementing SAP Business One today.