Master Data Preparation
One of the critical activities during the SAP Implementation project is preparation of company’s master data. Some of the key master data objects are
- Item Master
- Bill Of Material
- Customer Master
- Vendor Master
- Chart of Accounts
- Cost Centres
- Price Lists
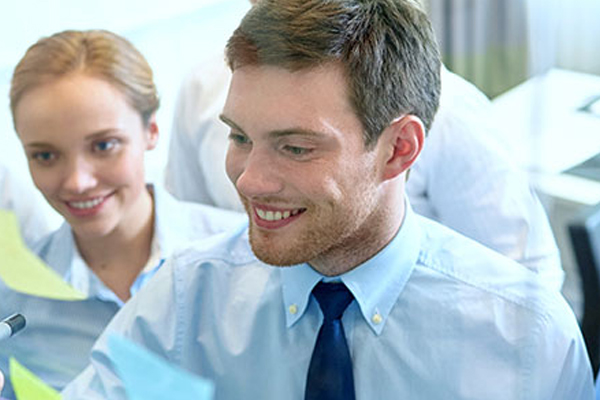
Whereas the implementation partner needs to guide the customer on the process to follow, templates to use, best practices etc., the primary ownership of creating this data lies with the customer, since it is their business and they would know their data the best. Having good quality data is one of the key success factors for the project. It is essential that the customer identifies the right people to work on this activity in order to maintain a consistency, accuracy and currency of the data. Even if a junior person from business or IT side is actually working on data preparation, a senior process owner needs to review the data carefully and own it before submitting to the SAP team.
If a company is already using some software to manage its business, it is likely to have some or all of the master data available in some form. Even in such case, it is important that the existing data is reviewed/re-visited ensure that only good quality data is passed on to SAP. In fact, customer should look at the SAP project as an opportunity to get the existing data cleaned up. Some of the commonly found issues with existing data include duplication of data, incorrect descriptions, incomplete records, inaccurate information and obsolete data.
Time taken for preparing good quality data depends on several factors. Some of the key factors are mentioned below in brief as examples:
SL.No. |
FACTOR |
IMPACT |
1 |
Nature of business |
A trading company may deal with only finished goods (or sometimes packing materials) whereas a manufacturing company deals with finished goods, raw materials, WIP stages, consumables etc. A company involved in offering services will have a different set of data related to the services. |
2 |
Number of products/SKUs |
More the number of products, more will be the item master and Bill of Material Data (for manufacturing companies) |
3 |
Number of interim production stages in the manufacturing process |
If company wants to track inventory lying in interim stages of production it has to provide for additional item masters and BOMs to reflect these stages. |
4 |
Variation in raw material |
Raw materials needed for manufacturing process will vary depending on product, processes, use of alternate materials etc. |
5 |
Number and Variety in Machines/Equipment (For manufacturing companies) |
This has an impact on the item master to the extent of material required for maintenance of equipment. It also has an impact on consumables used in the production process.
|
6 |
Knowledge level of the person/team |
If the team members are knowledgeable they can turn around the data faster and of higher quality as compared to someone who may be hired to ‘enter data’ by copying it from different sources. |
7 |
Time allotted to this activity |
It is recommended that the team/person working on master data should be dedicated for this activity along for a few days. If the person gets only limited time in a day to work on this, it is likely that data consistency gets effected in addition to taking more time to complete the entire activity |
In summary, partner needs to guide the customer appropriately so that customer can gauge the quantum of work correctly to begin with. After that the customer needs to identify the right team, allow them to work on master data preparation activity in a dedicated manner, give them sufficient time to create, review and cleanse existing data (if available) & finally populate the data templates diligently. Taking shortcuts here is very likely to have a far reaching impact on the implemented solution’s success.At Praxis, we handhold the customer carefully when it comes to master data preparation and explain the impact of this activity on the project. Further we get top management’s commitment to take required actions to ensure good quality data is delivered on time.To know more you can reach out to sales@praxisinfosolutions.com or call on +91-88050 25521/18/19. To know more about our company, please visit praxisinfosolutions.com