Whether you run a manufacturing company or distributorship or a retail outlet managing inventory efficiently is a must from both top line and bottom line perspective. Large enterprises would have taken required measures to manage their inventories, at least the basic management, probably couple of decades back and would be currently leveraging cutting edge technologies to implement very sophisticated solutions to catch up with changing trends. However, it may be shocking to know that close to 46% companies in the SME sector are still using pen and paper or simple excel files to manage this complex problem even today! Even in the western world! Could the problem be more widespread in India? Good chances of that being true, right?
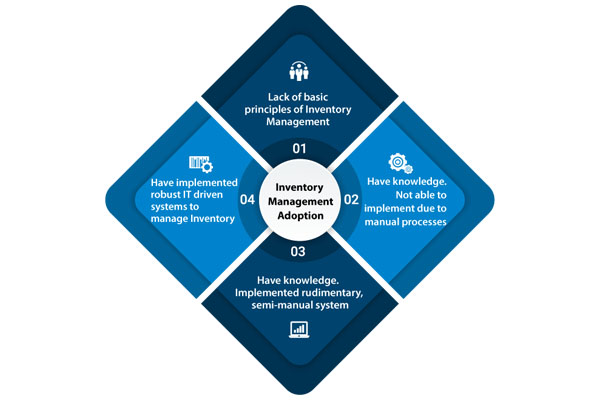
Categorization of SMEs with respect to adoption of modern Inventory Management techniques
A simple classification of companies from the SME sector with respect to their adoption of inventory management processes will look like this:
Categorization of SMEs with respect to adoption of IM techniques
Category 1- companies need to consider themselves lucky to have somehow survived till date. However, they need to start acting without losing any more time and learn the basic principles of inventory management and start implementing it with a clear road map to move to category 4 aggressively.
Category 4- companies are most likely trying to improve their systems even further and need to continue doing that to adapt to changes as needed depending on their nature of business. Companies in this category may find themselves at different stages of IT adoption in general. Some
companies may be using standalone inventory management software applications where as some other companies may be using more comprehensive systems. They need to assess whether their existing solution is scalable enough, whether it is integrated with other processes that touch inventory management processes like order fulfilment, quality management and so on.
Category 2 and 3- companies are at a point where they need to take a decisive step towards adopting Information Technology to address not only their inventory management issues, but to improve the way their entire operations are conducted. In fact, they should evaluate SAP Business One, a comprehensive, robust can scalable solution from SAP which has been developed keeping the SME sector in mind. Since we are talking on inventory management here, let us see how SAP Business One helps you adopt some of the fundamental best practices of inventory management.
Since we are talking on inventory management here, let us see how SAP Business One helps you adopt some of the fundamental best practices of inventory management.
Fundamental Best Practice |
How SAP Business One Helps in Adopting it |
Segregate different item types and maintain SKU numbering |
Items can be classified into multiple categories and every SKU can be uniquely traced with an item code |
Integrate with inward and outward transactions |
Stock quantities and values get updated with every Goods Receipt and Goods Issue
|
Maintain min-max levels for certain itemsbased on their value, criticality etc. |
Item master data in SAP Business One has a large set of parameters using which such levels and even more can be maintained. Automatic alerts can be generated as soon as levels are breached |
Identify trends of consumption like slow moving, fast moving etc. |
This can be handled very easily using reporting capabilities of the system |
Plan inventory levels in line with your projected consumption |
System offers a comprehensive MRP (Material Requirement Planning) functionality that will help companies to maintain the right inventory levels for various items be it finished goods or WIP items or even the lower most component of the BOM i.e. raw materials |
Track expiry dates or equivalent time dependent parameters of stocked items |
This can be handled very easily using reporting capabilities of the system. Not only tracking,but system can generate pro-active alerts which can help in taking timely actions. |
Integrate with bar-coding system |
SAP Business One system is developed in such a way that any integration with third party systems say barcoding in this case is easily possible. |
Perform cycle counting for certain items(backed by decisions like cycle counting frequency, counting strategy etc.) or physical stock verification for all items |
Cycle counting, physical stock take and reconciliation etc. are standard features. This capability helps companies keep close track of inventory levels in the company across several locations with a few clicks of mouse |
Conclusion
Category 2 and 3 companies must move forward quickly in adopting solutions that will enable them to manage inventory efficiently, accurately and in real time. SAP Business One is a world class ERP solution that addresses inventory management in line with the Best Practices. Not just this, it will help companies manage their entire operations like sales, purchase, production, stores, after sales, project management and Accounts & Finance.