New and Improved Production Module in SAP Business One
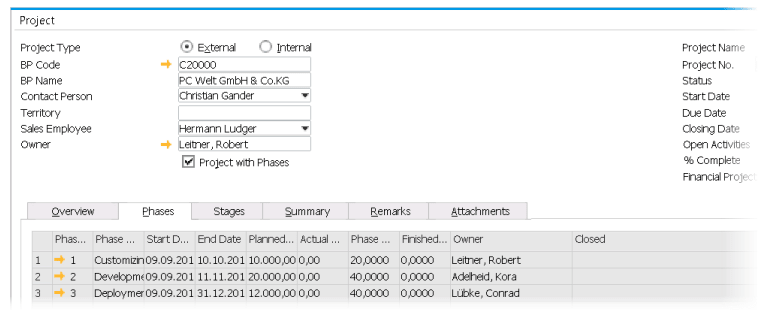
By Dattatreya R.Kulkarni Posted March 10, 2016 In Production
New and improved Production module
Till version 9.0 of Sap Business One, the bill of material (BOM) allowed the user to maintain only items as ‘child’ components. This allowed the user to:
- Maintain information about planned or expected consumption of child items to produce the parent item
- Transfer this information to the production order automatically and further allowing the user to update actual consumption (for manually issued items)
- Track variance in material consumed or produced, thus helping the user to extract a yield report
Whereas this did serve the purpose of bringing more accountability towards material consumption, it did pose a limitation when it came to consumption of non-item inputs consumed during the production process.
The SAP Business One 9.1 release includes a new production resources module, enhanced bill of materials and new production process options. With SAP Business One version 9.1 users can maintain the following two additional types of inputs (in addition to ‘item’) as child components in the BOM.
- Resources
- Text